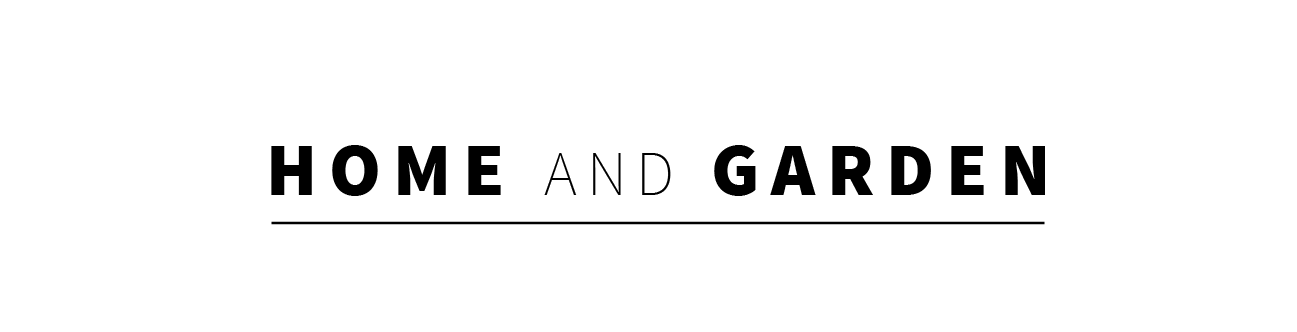
Set in Stone
WORDS BY KATHRYN JOHNSON PHOTOS BY KATHERINE IVES PHOTOGRAPHY
SPRING 2022
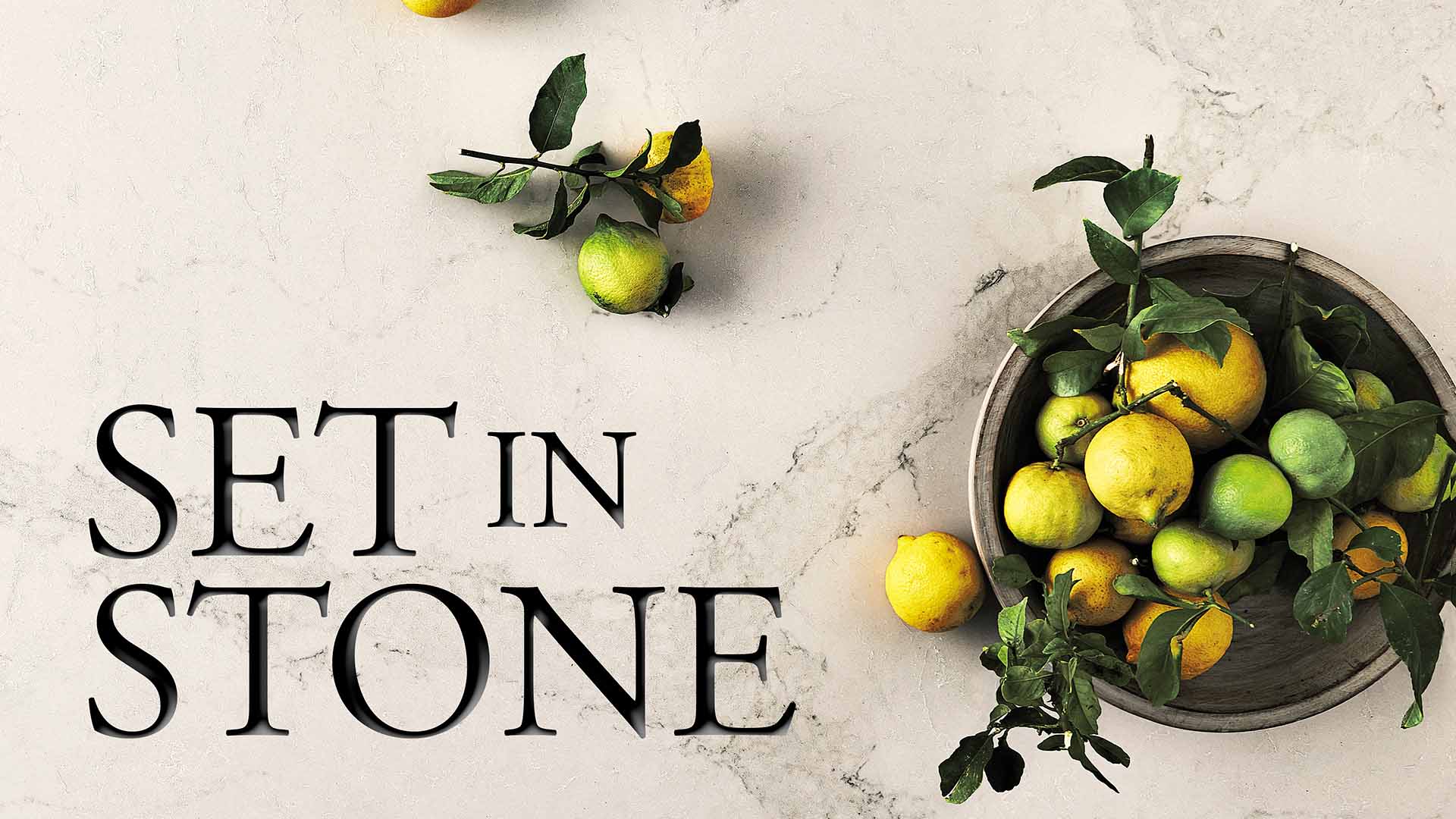
Love of local might be my favorite part of the culture at Caesarstone. The Israeli headquartered quartz manufacturing company opened their third manufacturing plant at the Belfast Commerce Center in Richmond Hill in 2015. Their intentions similar to most…to grow their footprint, maximize profits, and to enhance their mission and values— which are set in stone.
In 1987, Caesarstone pioneered the quartz countertop. Raw quartz is abundant in nature—common like sand and hard like steel—offering a durability like no other in the surface industry, advantages unattainable with marble, granite and things of the like. Using patented technology and desire for innovative design, Caesarstone grew quickly, attracting high-end interior designers around the world. Growing demand in the US made opening a manufacturing facility to expedite product-to-market a necessity, thus leading to the 2015 expansion. Today, Caesarstone has four manufacturing facilities in the US, India and Israel and they sell to 55 different countries globally.
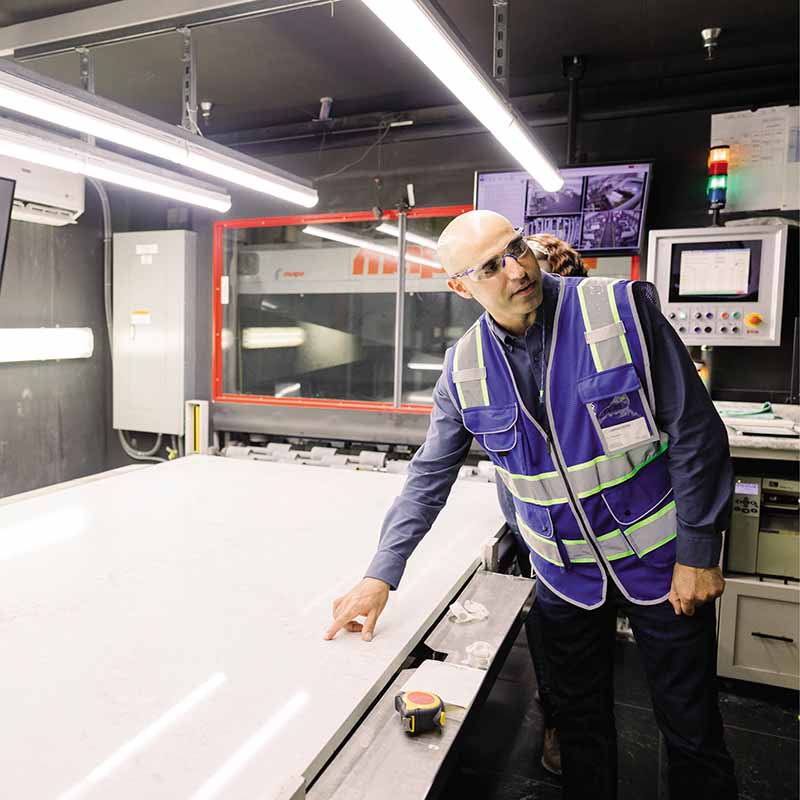
Yossi Binyamin, local Plant Manager, took me on a tour of the manufacturing facility recently. He showed me every nook and cranny of the plant, explaining the steps of production as we walked and introducing me to the people behind the scenes. The goals, machinery, future expansion budgets, replacement parts, finished product, logistical patterns, obviously very expansive, expensive, immensely complicated, but fascinating no doubt. But even more so impressive and unexpectedly obvious was the execution of the company’s four core values. “It’s the Caesarstone way,” Yossi explains pointing to the words painted on interior walls for all to see: Winning Spirit, People First, Accountability, and Innovation.
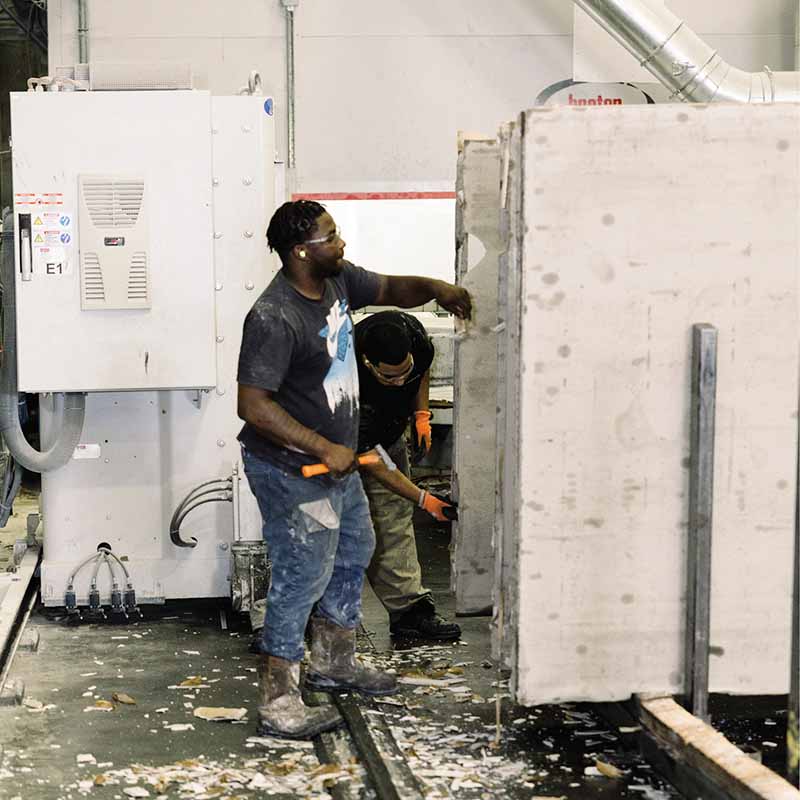
Yossi relates the manufacturing process to that of baking a cake. Slabs are mixed, poured, molded, and then baked to perfection. Extensive research led Caesarstone to learn that many of the ingredients needed in their process could be locally sourced instead of being imported, the trickle down effect creating more American jobs and sustainability— another win for the company’s success story on American soil. Quality control at Caesarstone requires a keen eye. Every stone is assessed for color consistency and pattern perfection, any deviation (most not even recognizable to the naked eye) results in the slab being labeled imperfect and not for market. These stones are moved to a yard onsite, many are shipped to markets seeking a lower grade stone. “Our collection of perfectly imperfect stones is impressive,” says Allen English, Associate Supply Chain Manager. I could not agree more. “We decided to explore an opportunity for locals to access Caesarstone. Our new outlet program allows you to buy directly from our yard.” My kitchen and bathroom just saw a surface renovation thanks to this program! The stone I chose had an imperfect edge easily cut off by local fabricators, Surface Setters.
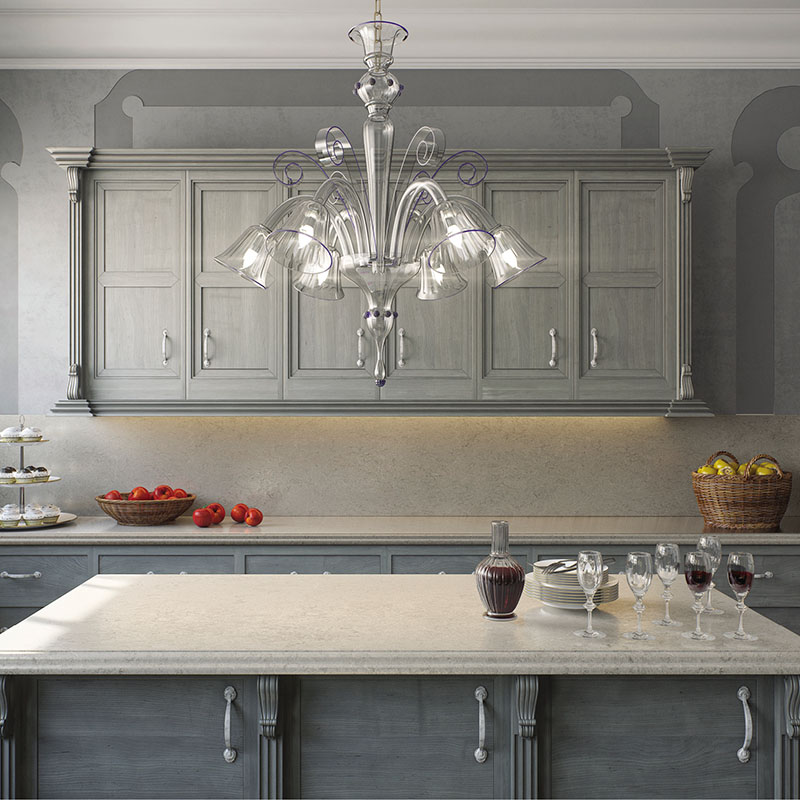
More impressive than what leaves the manufacturing plant by truck, rail or sea though is the people and the culture being shared inside. How a simple grain of sand has brought two worlds together to learn from each other and grow in a mutually beneficial way is as beautiful a story as the stones made there. Yossi says the initial concerns of being a part of the community are no longer concerning. “Richmond Hill has been good for us, and there is so much more to come.” They, too, love local; they are embracing it as a lifestyle, and giving back in so many ways. I am proud to have them in my home. Made in the USA. Made in Richmond Hill. Just think, a world-renowned product and culture growing within our community and using local people to do it.